Communication solution for hazardous areas
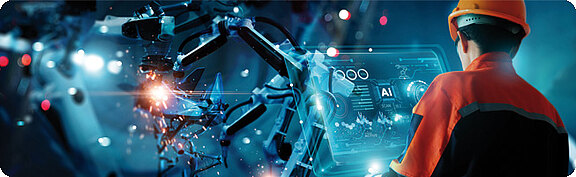
Ultra-compact communication solution for combining an endoscopic camera and a Kl.2 barcode scanner in hazardous areas
Project planning
In a mixing container for paints and varnishes it is not only dark and cramped, but there is also a risk of explosion (zone 0). A market leader in the field of dosing technology and expert in filling systems had different needs for dosing and filling processes. These machines are high-performance machines that are built to be ultra-compact. This means that we always need very compact solutions at this point. SAMCON uses 2 different types of device technology. One is an endoscopic camera. The other is a Class 2 barcode laser scanner. Make sure that no lumps form in the mixing container. At the customer's request, an explosion-proof endoscope camera was developed for process monitoring in the mixing container. An endoscopic camera based on the AXIS P13xx series without a lens was installed in our flameproof housing. Care was taken to ensure that the sensor was positioned exactly in the optical axis of the housing. A mounting adapter was installed outside the flameproof enclosure for connecting an Olympus borescope/endoscope via a fine thread.
This borescope/endoscope solution not only allows a wide variety of viewing angles, but also allows different directions for ultra-compact process room monitoring (seeing 90° around corners) using purely optical light guidance. With this solution you can look into ultra-compact process rooms. The borescope/endoscope solution is connected to the process room via a cable entry (KLE), while the electrical device technology is protected in the flameproof enclosure.
In addition, class 2 barcode scanners (devices which fall within the scope of DIN 60079-28, standard for optical radiation) were required to fill the paints and varnishes.
Several possible protection mechanisms are described in DIN 60079-28, in our case optical intrinsic safety [op is] is the essential one. It was checked in advance that the maximum light output that is emitted is not above a critical level. To verify this, we resorted to destructive tests. The precise examination of different light output stages and laser diodes was carried out in an accredited testing laboratory. We included this laser in our type testing and thus made it possible for our customer to have the first Class 2 laser in the Ex area. Both devices have an extremely high level of customization for the customer.
Testimonial:
“It was clear to us before the project planning began that our narrow process spaces and the barcode laser facility in the Ex-d area could not be solved with standard devices.
SAMCON not only delivers “off the shelf”, but also responds to our individual wishes to a high degree without jeopardizing explosion safety.”