Camera and Communication Systems in Process Control Systems
The Toughest Camera and Communication Technology Requirements in the Explosion Risk Zones of Process Control Systems
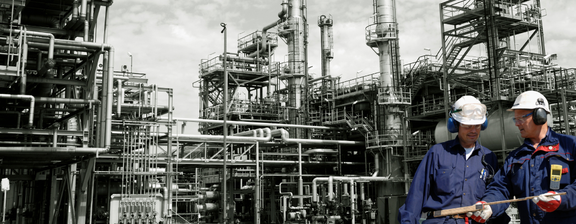
Thanks to modern control and process control systems, systems in the chemical industry now feature a high degree of automation, even in explosion risk zones. A wealth of different process factors are recorded in the field and visualised in plant measuring stations. But what is the situation actually like when it comes to centrifuges or disc dryers? Does the noise of a pump suggest a damaged bearing? To look into these and other questions, on-site inspections are regularly performed and a whole range of different sight glasses are examined. Camera and communication systems have found their way into automation technology:
Process Control Systems are learning to see, hear and speak!
Before 1960, measurements in chemical production plants were to the greatest extent performed on the premises. If you wanted to know, for instance, how high the temperature in a container is, you had to go on-site and read the local indicator. Final controlling devices and actuators, also located on-site, would then be adjusted in response to the value that was read. It was in the 1960s that the trend of automating these processes first of all with centralised, and subsequently with local, process control systems began. The measurements were converted into electrical signals, interpreted and displayed in a central plant measuring station. From there, actuators could be controlled – in a fully-automated or controlled manner or by way of manual intervention.
Today, recorders, switches and indicators have been replaced by visualisation stations. IT components are being assembled to form visualisation networks and Ethernet is breaking its way through as the transport medium of the future, right down to field level. Plant measuring stations belonging to several production plants are being combined and outlying locations are remote-controlled across long distances.
See and hear, what can not be measured.
What if modern measuring technology reaches its limits? What if it's not just the fill level of a tank that is decisive, but also whether foam or solid bodies float on the surface, like in the case of biomass fermenters, for instance? What if it is important to know whether the torch of an ethylene compressor station burns clean? What if, in the case of a gearbox, the bearing noise provides an important piece of information?
Even today, these critical questions are frequently still clarified by performing on-site inspections. Containers and equipment have sight glasses, which are examined during maintenance tours. As before 1960, the "sight" is then interpreted and appropriate measures introduced. In order to automate such "see - interpret - respond" chains, the option of mounting cameras in the field and monitors in the measuring station does not represent a solution. The monitors would indeed transmit the image to the measuring station, however the regular "viewing" and interpreting of the image would still be the responsibility of the human observer. It is more meaningful to integrate cameras, loudspeakers, microphones and headsets completely into the process control system, as was done with on-site measurements after 1960.
Field Devices: Cameras, Loudspeakers and Microphones.
In order to make video and audio signals available in process control systems, they first of all have to be accommodated on site. Camera requirements for explosion risk zones range from static systems with manually adjustable view angle (ExCam® vario) and high-performance motorised zoom cameras with rotatable IR blocking filter (ExCam® niteZoom), to dome camera systems with integrated DECT base station (ExCam® 360°). Depending on the project requirement, ATEX-certified loudspeakers, room microphones or headsets can be used for the audio connection. With this portfolio of field devices, there is a solution for practically all audiovisual communication tasks, from simple process monitoring, to securing a four-person work team, which operates using headsets and dome cameras under the constant audiovisual surveillance of the measuring station.
Local Peripheral Equipment: The Connection Rail Series
As a rule, cameras and microphones supply analogue signals (CVBS, LF audio). The job of the Connection Rail series is to convert these signals into digital network streams (see image 2). As part of the Connection Rail series, both ATEX-certified devices for use in explosion risk zones and non-ATEX devices for industrial switch cabinet environments are available. Once the video and audio data is converted and available on the Ethernet, there are no longer any limits with regard to usability. Functions such as camera control, layout plan navigation, the opening and closing of voice channels, recording and remote access are reduced to software requirements and no longer require any additional hardware!
Operating and Observing – Complete Integration in Process Control Systems.
As in the case of process control systems, camera and communication systems provide the system operator with key information for targeted intervention, too. The SAMCON®trol web server application prepares the image and control signals for this such that they can be called up from the PCS by URL. With this technology, the installation of video client software on the visualisation stations of the PCS is no longer required. The browser, be it installed on the operating system or integrated in the PCS, takes on all of its tasks. By way of dynamic HTML scripts (ViewScriptbox – see image 3), the user can individually compile the desired visualisation with layout plan navigation, grouped video thumbs; lists and recording archives. The pages created in this way can then be called up from the PCS manually or automatically (event triggered). Cameras can themselves detect movements in the image and inform the PCS.
Camera and communication systems have lost their special status in plant measuring stations. Cameras, headsets, loudspeakers and microphones are becoming process control sensors and actuators and are being seamlessly incorporated into the process control system. Recording, control and display of live images, as well as the opening and closing of voice channels, are becoming additional functions of the visualisation stations!
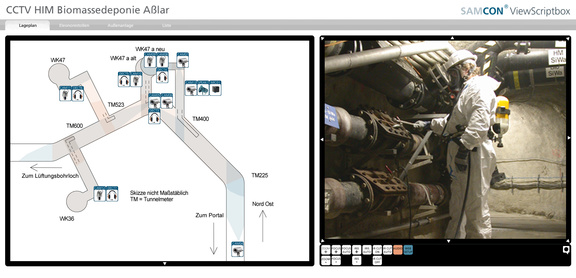